Choshitsu (Carved Lacquer) "Shinzan Shinku" Japanese traditional techniques
Choshitsu (Carved Lacquer) "Shinzan Shinku" Japanese traditional techniques
Our Selling Price: US$8,000.00(tax excluded)
Item Description
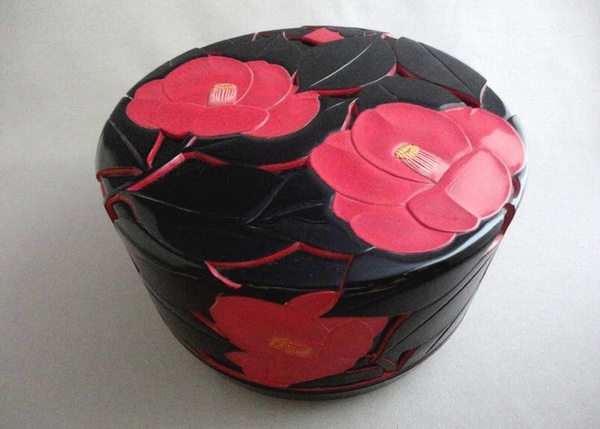
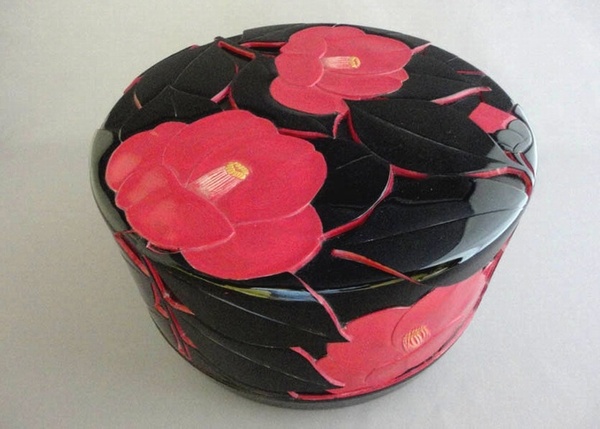
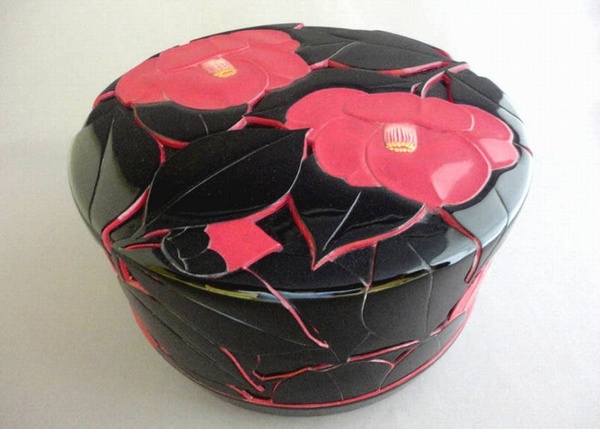
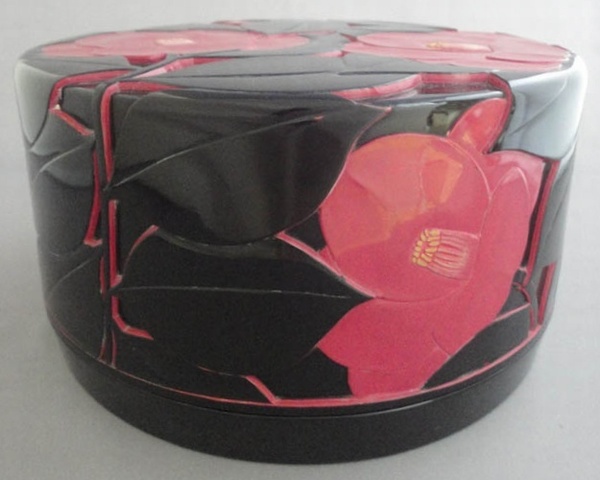
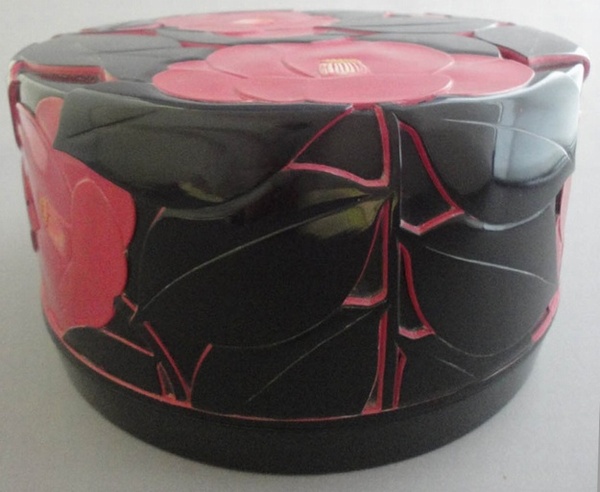
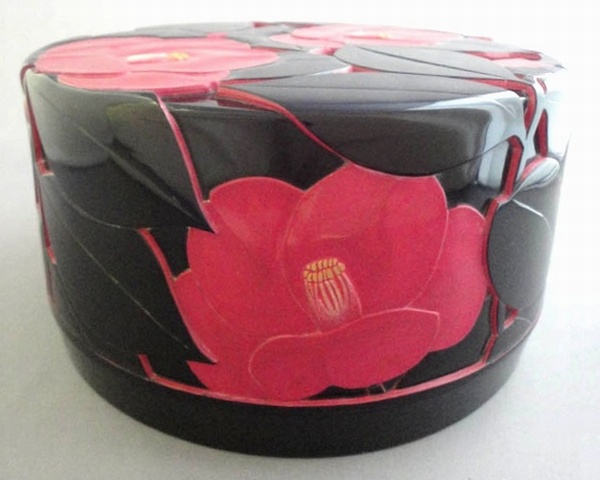
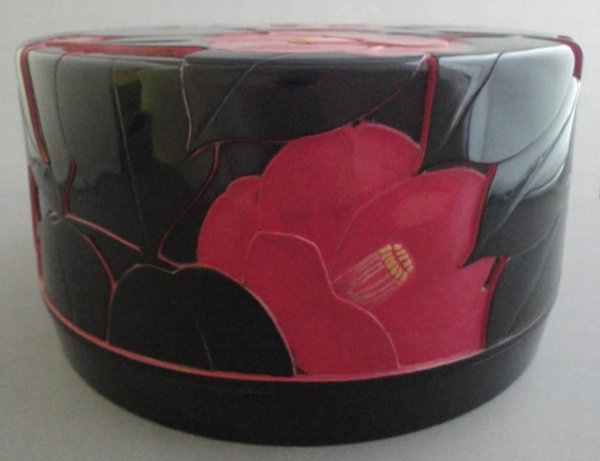
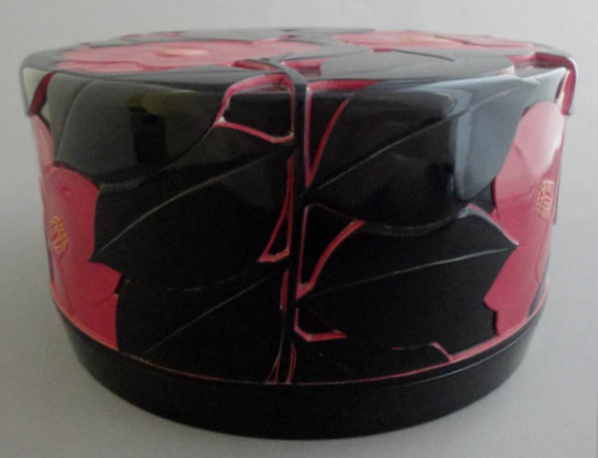
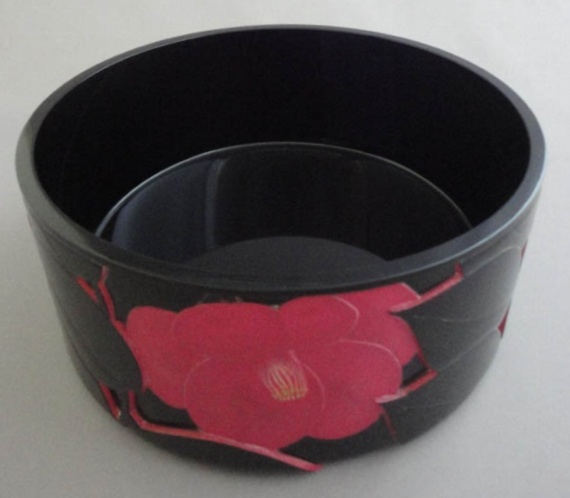
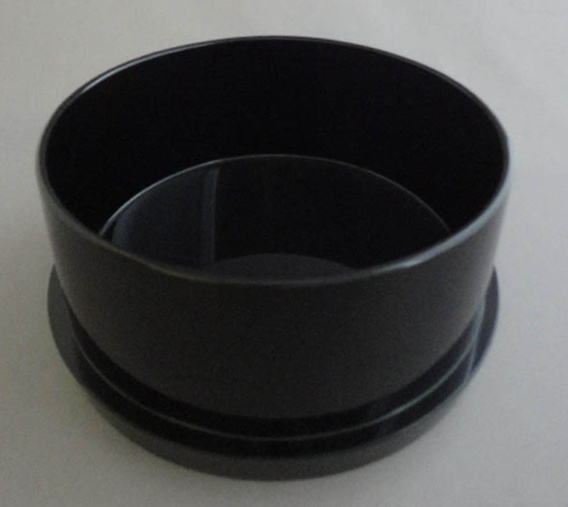
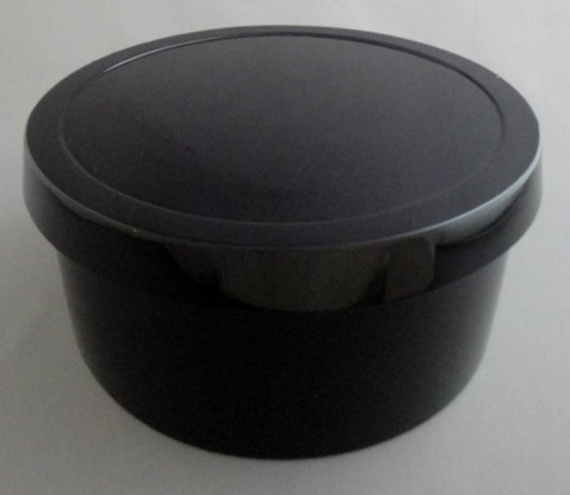
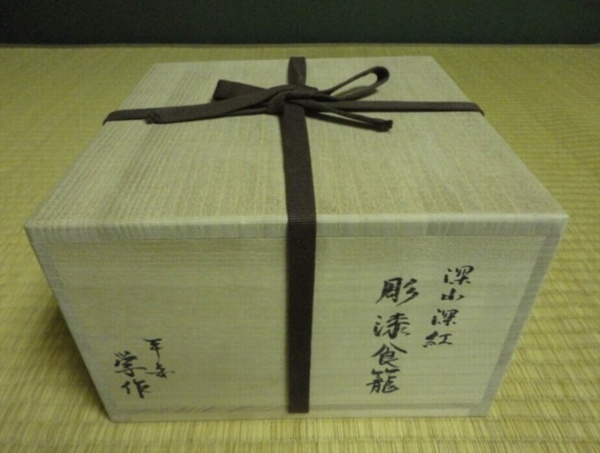
We have just added some Choshitsu (Carved Lacquer) items made with Japanese traditional techniques to our shop.
Please enjoy the traditional master craftsmanship thoroughly.
About Choshitsu:
Choshitsu is a lacquer technique started in China originally. It is the technique that many layers of lacquer are applied and then designs are engraved on them.
Tsuikoku is the one carved and layered only in black lacquer whereas Tsuishu is the one carved and layered only in red lacquer. As a generic term, any layered lacquer carved is called Choshitsu.
It is a traditional work of art which takes at least half a year to make.
This work of art, Choshitsu, is relatively unknown even in Japan where only a few people would know. Decorative Boxes, trays, incense burners, tables, Japanese tea sets created by using these Choshitsu techniques were very much treasured during the Muromachi period.
How to create Choshitsu
1. First create a wooden base:
Make a mold with wood and process it using.
Sashimono (woodworking joinery without using nails) as well as Hikimono (woodturning with woodturning machines).
2. Paint base layers of lacquer:
Paint base layers of lacquer on the wooden base.
3. Apply layers of lacquer to a thickness of about 3 mm (300 times of applications are required to create a 3mm thickness and it can be applied only once a day):
Depending on designs, so many different colors of lacquer such as black, red and so on are layered. Sometimes different colors of lacquer are applied and layered so they can create stripes.
4. Designs are engraved on the surface of layered lacquer:
Trace a design and engrave along with it on the layered lacquer with Choshitsu engravers. The more layered (many layers) the lacquer is, the more stereoscopic and sublime engraving will be attained.
5. Polish it to make it lustrous:
Polish the engraved surface with polishing agent.
Some parts are not polished whereas other parts are polished so that the finished product may get the stereoscopic depth to it.
Production Process:
1. The process of building layered lacquer:
Layers of colored lacquer are painted on the Paulownia box and then dry them. Repeat this process numerous times so that the craftsmen may achieve the desirable volume of layered lacquer.
Once a craftsman achieves the desirable volume of layered lacquer, carving will be done.
Polish the carved surface, especially the raised parts, in order to create more three dimensional impression by using whetstones in the following order of rough whetstones first, and then medium whetstones and finally fine whetstones with polishing powders.
4. The yellow parts (the stamen and pistil) of the camellia flowers:
Once the production process up to the Polishing Process is complete, the yellow part(Pistils) is polished again by using the rough whetstones and then sticky raw lacquer (raw lacquer solution) is applied. Keshikin process (fine genuine 24 K gold powder finer than size 1 is sprinkled) is done on top of that.
The Production Process of the Inner Part of the Paulownia Box (Kuro-roiro Lacquer Finish):
Polish the inner part of the Paulownia box which has been painted with Kuro-roiro lacquer and make it lustrous by varnishing. It is also called Kyomen Shiage (mirror finish) as the polished surface reflects the light and matters just like a mirror.
Please enjoy the traditional master craftsmanship thoroughly.
About Choshitsu:
Choshitsu is a lacquer technique started in China originally. It is the technique that many layers of lacquer are applied and then designs are engraved on them.
Tsuikoku is the one carved and layered only in black lacquer whereas Tsuishu is the one carved and layered only in red lacquer. As a generic term, any layered lacquer carved is called Choshitsu.
It is a traditional work of art which takes at least half a year to make.
This work of art, Choshitsu, is relatively unknown even in Japan where only a few people would know. Decorative Boxes, trays, incense burners, tables, Japanese tea sets created by using these Choshitsu techniques were very much treasured during the Muromachi period.
How to create Choshitsu
1. First create a wooden base:
Make a mold with wood and process it using.
Sashimono (woodworking joinery without using nails) as well as Hikimono (woodturning with woodturning machines).
2. Paint base layers of lacquer:
Paint base layers of lacquer on the wooden base.
3. Apply layers of lacquer to a thickness of about 3 mm (300 times of applications are required to create a 3mm thickness and it can be applied only once a day):
Depending on designs, so many different colors of lacquer such as black, red and so on are layered. Sometimes different colors of lacquer are applied and layered so they can create stripes.
4. Designs are engraved on the surface of layered lacquer:
Trace a design and engrave along with it on the layered lacquer with Choshitsu engravers. The more layered (many layers) the lacquer is, the more stereoscopic and sublime engraving will be attained.
5. Polish it to make it lustrous:
Polish the engraved surface with polishing agent.
Some parts are not polished whereas other parts are polished so that the finished product may get the stereoscopic depth to it.
[Description]
Name: | Shinzan Shinku |
Origin: | Kyoto, Japan |
Size: | 11cm * 21cm * 21cm(H*W*D) |
Weight: | 1,116g |
Technique: | Choshitsu |
Materials: | Zelkova |
Numbers of applications of lacquer: | 85 times |
Shipping: | FREE SHIPPING! |
1. The process of building layered lacquer:
Layers of colored lacquer are painted on the Paulownia box and then dry them. Repeat this process numerous times so that the craftsmen may achieve the desirable volume of layered lacquer.
- When lacquer is applied 100 times, the thickness will become about 3mm (which will take approximately 100 days).
- One application per day only (as it takes time to get the lacquer dry)
- The layers of lacquer have been applied on this product (Camellia) 85 times:
black lacquer is applied 15 times → red lacquer is applied 20 times → black lacquer is applied 5 times → red lacquer is applied 40 times → black lacquer is applied 5 times.
Once a craftsman achieves the desirable volume of layered lacquer, carving will be done.
- The camellias on the top of the box are carved at the point of "red lacquer is applied 40 times" whereas the camellias on the sides of the box are carved at the point of "red lacquer is applied 20 times". The reason why carving was done separately at the different stages of painting is for the product to have the stereoscopic depth to it by painting “black lacquer 5 times → red lacquer is 40 times → "black lacquer 5 times", altogether 50 times, on the camellias of the sides.
- The camellias and leaves on the side, and the camellias and leaves on the top of the box are engraved at the different stages of the production process: the former at the point of the middle stage of "black lacquer is applied 5 times" and the latter at the point of the very last stage of "black lacquer is applied 5 times".
- Leaves on the top of the box are carved at the point of the last stage of "black lacquer is applied 5 times" and therefore the red color framing the leaves was not painted at a later stage but painted at the point of "red lacquer is applied 40 times". This is a distinctive characteristic of Choshitsu.
- The first stage of painting, "black lacquer is applied 15 times", is to prevent the wooden base to be revealed by carving.
Polish the carved surface, especially the raised parts, in order to create more three dimensional impression by using whetstones in the following order of rough whetstones first, and then medium whetstones and finally fine whetstones with polishing powders.
4. The yellow parts (the stamen and pistil) of the camellia flowers:
Once the production process up to the Polishing Process is complete, the yellow part(Pistils) is polished again by using the rough whetstones and then sticky raw lacquer (raw lacquer solution) is applied. Keshikin process (fine genuine 24 K gold powder finer than size 1 is sprinkled) is done on top of that.
The Production Process of the Inner Part of the Paulownia Box (Kuro-roiro Lacquer Finish):
Polish the inner part of the Paulownia box which has been painted with Kuro-roiro lacquer and make it lustrous by varnishing. It is also called Kyomen Shiage (mirror finish) as the polished surface reflects the light and matters just like a mirror.
- Kuro-roiro Lacquer:
Roiro Lacquer is lacquer which makes the surface lustrous and Kuro-roiro lacquer is the black Roiro lacquer. After coating with it, the products will be polished and varnished to make them shiny and lustrous. It is also called Kyomen Shiage (mirror finish) as the polished surface reflects the light and matters just like a mirror.
[The Profile of Choshitsu Artist Gaku]
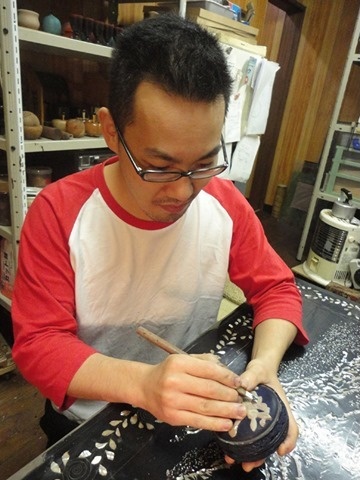
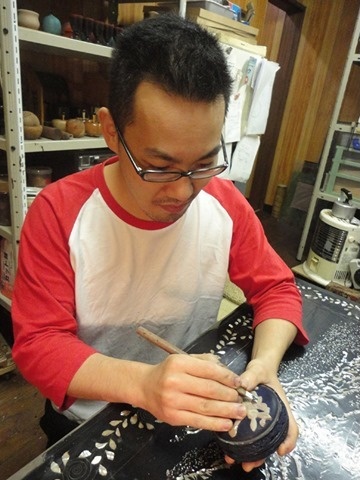
1978 | Gaku was born in Kyoto, Japan |
2002 | He graduated from St. Andrews University in Osaka and started to get trained at Ishikawa Prefecture Lacquerware-skill Training Center in Yamanaka where he learnt Rokuro (woodworking) skills. |
2003 | His work got accepted at Craft Competition in Takaoka |
2006 | He completed training at Ishikawa Prefecture Lacquerware-skill Training Center in Yamanaka and started to train at Kagawa Prefecture Urushi Lacquer Ware Institute where he learnt lacquer painting and Choshitsu. |
2009 | He completed training at Kagawa Prefecture Urushi Lacquer Ware Institute and moved back to Kyoto and started to be engaged in the family business of lacquer production. He was in charge of Mokuji (Wood Base), painting and Choshitsu of Sashimono (woodworking joinery without using nails) at Manju Lacquer Studio. His work got accepted at the 49th Japan Crafts Exhibition. |
2012 | His work got accepted at the 41st Traditional Craft Kinki Area Exhibition. |
2013 | His work got accepted at the 42nd Traditional Craft Kinki Area Exhibition. His work got accepted at the 59th All Kansai Exhibition. |